home elevator factory, once a luxury for a select few, have become an integral part of modern residential design, offering accessibility, convenience, and a touch of elegance. The process of manufacturing these sophisticated systems involves meticulous engineering and innovative technology. This article provides an inside look at how home elevators are crafted in factories, highlighting the key stages of production and the innovations driving the industry.
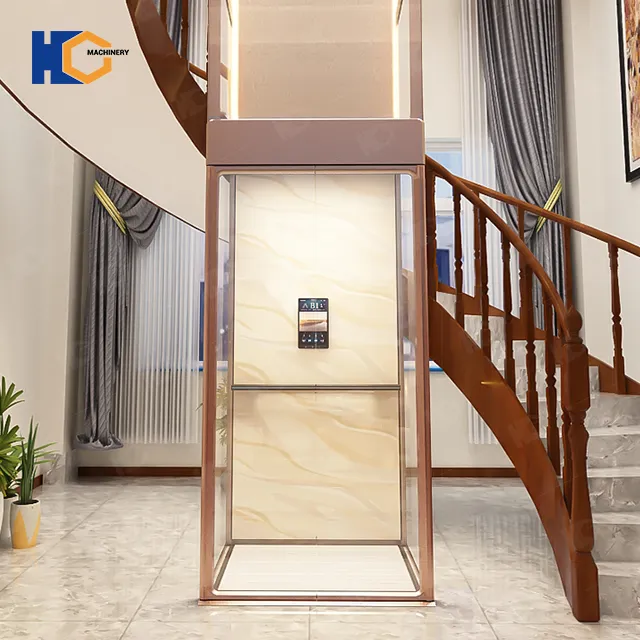
The Manufacturing Process: From Concept to Completion
- Design and Engineering
- Concept Development: The journey of a home elevator begins with conceptual design. Engineers and designers work together to create elevators that fit various residential needs, from compact models for smaller homes to grander systems for larger estates. The design process ensures that the elevator integrates seamlessly with the home’s architecture and meets the client’s requirements.
- Customization: Factories offer extensive customization options to match different tastes and home styles. Clients can choose from various materials, finishes, cabin configurations, door types, and control systems, allowing for a personalized and aesthetically pleasing product.
- Technical Specifications: Detailed engineering plans are developed to guarantee that the elevator meets all safety and performance standards. This involves load calculations, safety feature integration, and compatibility with the home’s existing structure.
- Material Selection and Procurement
- Quality Materials: The choice of materials is critical for both durability and visual appeal. Factories use high-quality materials such as stainless steel, tempered glass, and aluminum to ensure that the elevators are robust and stylish.
- Sustainable Practices: Many factories are committed to sustainability by selecting eco-friendly materials and employing manufacturing processes that minimize environmental impact.
- Manufacturing and Assembly
- Component Fabrication: In the factory, various elevator components—including the cabin, doors, control panels, and mechanical systems—are fabricated with precision. Advanced machinery is used to cut, shape, and assemble these components to exact specifications.
- Assembly Process: The assembly process blends automated systems with skilled craftsmanship. Each component is carefully put together to ensure that the final product operates smoothly and safely. Quality control checks are performed throughout to maintain high standards.
- Quality Control and Testing
- Rigorous Testing: Each elevator undergoes extensive testing to ensure it meets all operational and safety standards. Tests include load testing, emergency simulations, and thorough inspections of mechanical and electrical systems.
- Compliance with Standards: Factories ensure that their elevators comply with both national and international safety regulations. This includes certification for safety features such as emergency brakes, backup power systems, and fail-safes.
- Final Customization and Finishing
- Personalized Details: After passing quality control, the elevator undergoes final customization. This stage involves adding bespoke features such as custom cabin interiors, specialized lighting, and advanced control systems tailored to the client’s specifications.
- Final Inspection: A final inspection ensures that the elevator is in perfect working order and meets all functional and aesthetic requirements before it is prepared for shipment.
- Packaging and Shipping
- Secure Packaging: To protect the elevator during transport, it is carefully packaged. Special attention is given to ensure that all components are securely packed to prevent damage.
- Global Logistics: Factories often ship elevators worldwide, necessitating efficient logistics to deliver the product to homes around the globe. The elevators are typically shipped in parts and assembled on-site by trained professionals.
Innovations in Home Elevator Manufacturing
- Smart Technology Integration
- Advanced Features: Modern home elevators are increasingly equipped with smart technology. Features such as touchscreens, voice controls, and remote monitoring enhance convenience and control for homeowners.
- Energy Efficiency: Innovations in energy efficiency, such as regenerative drives and LED lighting, help reduce energy consumption and operational costs.
- Modular and Adaptable Design
- Flexible Configurations: Modular elevator systems can be adapted to fit various home layouts and architectural styles. This flexibility allows for a wide range of design options and simplifies the installation process.
- Luxury Enhancements: For high-end markets, factories offer luxury options like custom wood paneling, panoramic glass cabins, and integrated entertainment systems, adding a touch of sophistication to the elevator experience.
- Focus on Safety and Compliance
- Cutting-Edge Safety Features: Factories prioritize safety by incorporating the latest technologies, such as advanced braking systems and emergency power backups.
- Adherence to Standards: To ensure global compatibility, factories adhere to international safety standards and certifications, ensuring that elevators are safe and reliable no matter where they are installed.
Conclusion: The Art and Science of Home Elevator Manufacturing
A home elevator factory is a place where cutting-edge technology, meticulous engineering, and skilled craftsmanship converge to create products that enhance the quality of modern living. From the initial design phase to final inspection and delivery, every aspect of the manufacturing process is carefully managed to produce elevators that are not only functional but also elegant and tailored to the homeowner’s needs. As demand for home elevators continues to rise, these factories remain at the forefront of delivering innovative solutions that blend safety, efficiency, and luxury.